ปัจจุบันกระจกแผ่นในโลกมี 3 ประเภท ได้แก่ กระจกแผ่นเรียบ กระจกลอย และกระจกรีด กระจกลอยซึ่งคิดเป็นมากกว่า 90% ของการผลิตกระจกทั้งหมดในปัจจุบัน ถือเป็นวัสดุพื้นฐานสำหรับการก่อสร้างกระจกสถาปัตยกรรมของโลก กระบวนการผลิตกระจกลอยก่อตั้งขึ้นในปี 1952 ซึ่งกำหนดมาตรฐานระดับโลกสำหรับการผลิตกระจกคุณภาพสูง กระบวนการกระจกลอยประกอบด้วยขั้นตอนหลัก 5 ขั้นตอน ดังนี้
● ส่วนผสม
● การละลาย
● การขึ้นรูปและการเคลือบ
● การอบอ่อน
● การตัดและบรรจุภัณฑ์
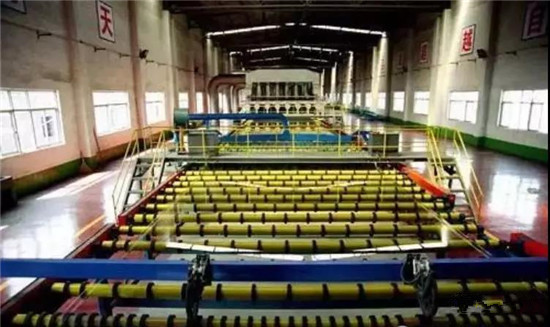
วัตถุดิบ
การผสมเป็นขั้นตอนแรกซึ่งเตรียมวัตถุดิบสำหรับการหลอม วัตถุดิบได้แก่ ทราย โดโลไมต์ หินปูน โซดาแอช และมิราบิไลต์ ซึ่งขนส่งด้วยรถบรรทุกหรือรถไฟ วัตถุดิบเหล่านี้จะถูกเก็บไว้ในห้องผสมวัตถุดิบ มีไซโล ถังบรรจุ สายพานลำเลียง รางเก็บฝุ่น และระบบควบคุมที่จำเป็นในห้องวัสดุ ซึ่งควบคุมการขนส่งวัตถุดิบและการผสมวัตถุดิบเป็นชุด วัตถุดิบจะเคลื่อนที่ตลอดเวลาตั้งแต่วินาทีที่ส่งวัตถุดิบไปยังห้องวัสดุ
ภายในห้องผสมวัตถุดิบ สายพานลำเลียงแบนยาวจะลำเลียงวัตถุดิบจากไซโลของวัตถุดิบต่างๆ ไปยังชั้นลิฟต์ถังตามลำดับ จากนั้นจึงส่งไปยังอุปกรณ์ชั่งน้ำหนักเพื่อตรวจสอบน้ำหนักของวัสดุผสม เศษแก้วรีไซเคิลหรือเศษแก้วที่ส่งกลับมาจากสายการผลิตจะถูกเพิ่มลงในส่วนผสมเหล่านี้ แต่ละชุดจะมีเศษแก้วประมาณ 10-30% วัสดุแห้งจะถูกเติมลงในเครื่องผสมและผสมให้เข้ากันในชุดผสม ชุดผสมจะถูกส่งจากห้องผสมวัตถุดิบไปยังไซโลหัวเตาเผาเพื่อจัดเก็บผ่านสายพานลำเลียง จากนั้นจึงเติมลงในเตาเผาด้วยอัตราที่ควบคุมโดยตัวป้อน

ส่วนประกอบของแก้วโดยทั่วไป
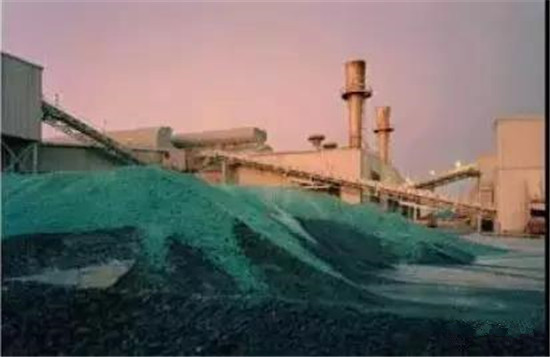
ลานเศษแก้ว
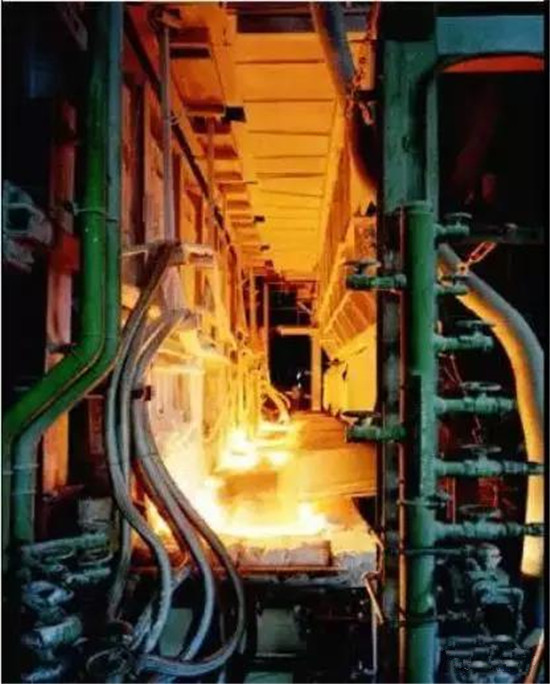
ป้อนวัตถุดิบที่ผสมแล้วเข้าไปในทางเข้าเตาเผาด้วยถังเก็บที่อุณหภูมิสูงสุด 1,650 องศา
การละลาย
เตาเผาแบบทั่วไปคือเตาเผาเปลวไฟขวางที่มีเครื่องกำเนิดใหม่ 6 เครื่อง กว้างประมาณ 25 เมตรและ 62 เมตร โดยมีกำลังการผลิต 500 ตันต่อวัน ส่วนหลักของเตาเผา ได้แก่ สระหลอมโลหะ/เครื่องตกตะกอน สระทำงาน เครื่องกำเนิดใหม่ และเตาเผาขนาดเล็ก ตามที่แสดงในรูปที่ 4 เตาเผาทำจากวัสดุทนไฟพิเศษและมีโครงสร้างเหล็กที่โครงด้านนอก ชุดวัตถุดิบจะถูกส่งไปยังสระหลอมโลหะของเตาเผาโดยตัวป้อน และสระหลอมโลหะจะได้รับความร้อนถึง 1,650 ℃ โดยปืนพ่นก๊าซธรรมชาติ
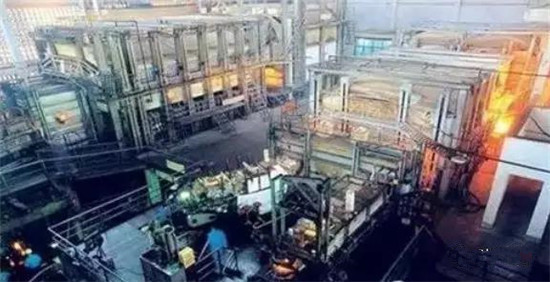
แก้วที่หลอมละลายจะไหลจากบ่อหลอมละลายไปยังบริเวณคอผ่านเครื่องตกตะกอนและถูกกวนอย่างสม่ำเสมอ จากนั้นจะไหลเข้าสู่ส่วนที่ทำงานและค่อยๆ เย็นลงเหลือประมาณ 1,100 องศาเพื่อให้ได้ความหนืดที่เหมาะสมก่อนจะถึงอ่างดีบุก
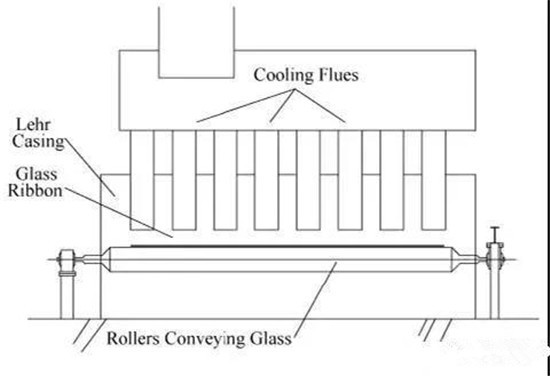
การขึ้นรูปและการเคลือบ
กระบวนการขึ้นรูปแก้วเหลวที่ผ่านการทำให้บริสุทธิ์เป็นแผ่นแก้วเป็นกระบวนการของการจัดการทางกลตามแนวโน้มตามธรรมชาติของวัสดุและความหนาตามธรรมชาติของวัสดุนี้คือ 6.88 มม. แก้วเหลวไหลออกจากเตาผ่านพื้นที่ช่องทางและการไหลจะถูกควบคุมโดยประตูที่ปรับได้ที่เรียกว่าแรมซึ่งอยู่ลึกประมาณ ± 0.15 มม. เข้าไปในแก้วเหลว แก้วลอยอยู่บนดีบุกหลอมเหลว ดังนั้นจึงเรียกว่ากระจกลอย แก้วและดีบุกไม่ทำปฏิกิริยากันและสามารถแยกออกจากกัน ความต้านทานซึ่งกันและกันในรูปแบบโมเลกุลทำให้กระจกเรียบขึ้น
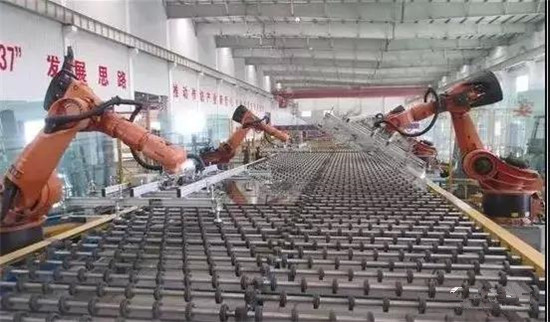
อ่างเป็นหน่วยที่ปิดผนึกในบรรยากาศไนโตรเจนและไฮโดรเจนที่ควบคุมไว้ ประกอบด้วยเหล็กรองรับ เปลือกด้านบนและด้านล่าง วัสดุทนไฟ ดีบุกและองค์ประกอบความร้อน บรรยากาศที่ลดลง เซ็นเซอร์อุณหภูมิ ระบบควบคุมกระบวนการคอมพิวเตอร์ กว้างประมาณ 8 เมตรและยาว 60 เมตร และความเร็วของสายการผลิตสามารถเข้าถึง 25 เมตรต่อนาที อ่างดีบุกประกอบด้วยดีบุกบริสุทธิ์เกือบ 200 ตัน โดยมีอุณหภูมิเฉลี่ย 800 ℃ เมื่อแก้วสร้างชั้นบางๆ ที่ปลายทางเข้าอ่างดีบุก จะเรียกว่าแผ่นแก้ว และชุดตัวดึงขอบที่ปรับได้จะทำงานทั้งสองด้าน ผู้ปฏิบัติงานใช้โปรแกรมควบคุมเพื่อตั้งค่าความเร็วของเตาเผาอบอ่อนและเครื่องดึงขอบ ความหนาของแผ่นแก้วสามารถอยู่ระหว่าง 0.55 ถึง 25 มม. องค์ประกอบความร้อนพาร์ติชั่นด้านบนใช้เพื่อควบคุมอุณหภูมิของแก้ว เมื่อแผ่นแก้วไหลผ่านอ่างดีบุกอย่างต่อเนื่อง อุณหภูมิของแผ่นแก้วจะค่อยๆ ลดลง ทำให้แก้วแบนและขนานกัน ณ จุดนี้ สามารถใช้ acuracoat ® ในการชุบฟิล์มสะท้อนแสง ฟิล์ม low e ฟิล์มควบคุมแสงอาทิตย์ ฟิล์มโฟโตวอลตาอิค และฟิล์มทำความสะอาดตัวเองบนอุปกรณ์ CVD แบบไพโรไลซิสได้ ณ จุดนี้ กระจกก็พร้อมที่จะเย็นลงแล้ว
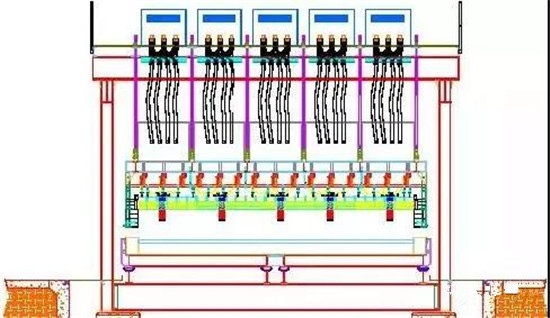
หน้าตัดอ่างอาบน้ำ
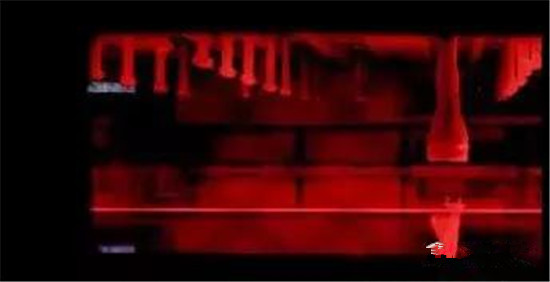
แก้วถูกกระจายเป็นชั้นบางๆ บนดีบุกหลอมละลาย แยกออกจากดีบุก และขึ้นรูปเป็นแผ่น
องค์ประกอบความร้อนแบบแขวนทำหน้าที่จ่ายความร้อน ส่วนความกว้างและความหนาของกระจกจะถูกควบคุมด้วยความเร็วและมุมของตัวดึงขอบ
การอบอ่อน
เมื่อแก้วที่ขึ้นรูปแล้วออกจากอ่างดีบุก อุณหภูมิของแก้วจะอยู่ที่ 600 ℃ หากแผ่นแก้วเย็นลงในบรรยากาศ พื้นผิวของแก้วจะเย็นลงเร็วกว่าภายในแก้ว ซึ่งจะทำให้พื้นผิวถูกอัดแน่นอย่างรุนแรงและเกิดความเครียดภายในที่เป็นอันตรายของแผ่นแก้ว
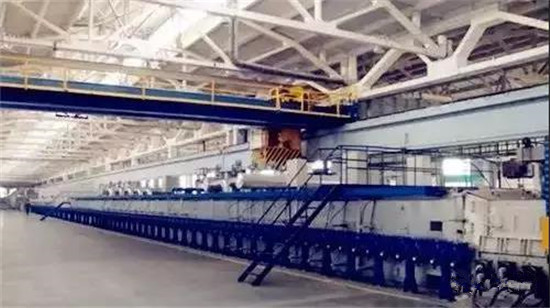
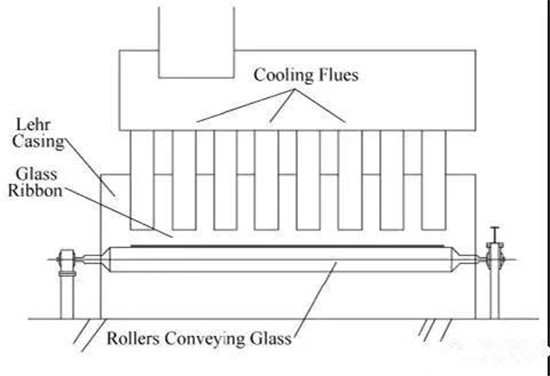
ส่วนของเตาเผาอบ
กระบวนการให้ความร้อนกับแก้วก่อนและหลังการขึ้นรูปเป็นกระบวนการของการสร้างความเครียดภายในด้วย ดังนั้น จึงจำเป็นต้องควบคุมความร้อนเพื่อลดอุณหภูมิของแก้วลงทีละน้อยจนถึงอุณหภูมิแวดล้อม นั่นคือ การอบอ่อน ในความเป็นจริง การอบอ่อนจะดำเนินการในเตาเผาที่มีการไล่ระดับอุณหภูมิที่ตั้งไว้ล่วงหน้า (ดูรูปที่ 7) กว้างประมาณ 6 เมตรและยาว 120 เมตร เตาเผาแบบอบอ่อนประกอบด้วยองค์ประกอบความร้อนและพัดลมที่ควบคุมด้วยไฟฟ้าเพื่อให้การกระจายอุณหภูมิในแนวขวางของแผ่นแก้วมีเสถียรภาพ
ผลลัพธ์ของกระบวนการอบอ่อนคือกระจกจะได้รับการทำให้เย็นลงอย่างระมัดระวังจนถึงอุณหภูมิห้องโดยไม่มีความเครียดหรือความเครียดชั่วคราว
การตัดและบรรจุภัณฑ์
แผ่นแก้วที่เย็นตัวด้วยเตาเผาจะถูกขนส่งไปยังพื้นที่การตัดผ่านโต๊ะลูกกลิ้งที่เชื่อมต่อกับระบบขับเคลื่อนของเตาเผา กระจกจะผ่านระบบตรวจสอบออนไลน์เพื่อขจัดข้อบกพร่องใดๆ และจะถูกตัดด้วยล้อตัดเพชรเพื่อเอาขอบกระจกออก (วัสดุขอบจะถูกรีไซเคิลเป็นกระจกที่แตก) จากนั้นจึงตัดให้ได้ขนาดตามที่ลูกค้าต้องการ โรยผงเคลือบพื้นผิวกระจกเพื่อให้สามารถวางซ้อนและจัดเก็บแผ่นแก้วได้เพื่อหลีกเลี่ยงการติดกันหรือรอยขีดข่วน จากนั้น แผ่นแก้วที่ไม่มีตำหนิจะถูกแบ่งออกเป็นกองเพื่อบรรจุหีบห่อด้วยเครื่องจักรแบบแมนนวลหรืออัตโนมัติ จากนั้นจึงถ่ายโอนไปยังคลังสินค้าเพื่อจัดเก็บหรือจัดส่งให้กับลูกค้า
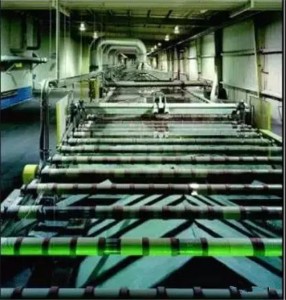
หลังจากแผ่นแก้วออกจากเตาเผาแบบอบ แผ่นแก้วจะถูกขึ้นรูปอย่างสมบูรณ์และเคลื่อนย้ายไปยังบริเวณที่ทำให้เย็นลงเพื่อลดอุณหภูมิต่อไป